Extrusion
AMS operates as a leading aluminium profile extruder with three state of the art extrusion presses. Our in-house extrusion capabilities allow us to not only produce our range of standard profiles but also offer tailor-made aluminium profiles. Control over the extrusion process enables us to cater to non-standard lengths, an approach that minimises wastage and optimises efficiency, especially for substantial contracts.
AMS’ production capacity is capable of exceeding 300 tons of extrusion per week. After extrusion, our aluminium alloy undergoes an aging and strengthening process via heat treatment. Once this step is completed, the resulting aluminium profiles are ready for delivery to the customer or can seamlessly progress to additional processes within AMS. These processes include but are not limited to painting, anodising, decoral, thermal break, or sheet metal fabrication.
Our extrusion business supplies many sectors including but not limited to aerospace, engineering, renewable energies, and transportation. This diversification has not only solidified our support to crucial industries but has also paved the way for significant export opportunities. Our reach extends to various markets in Europe, as well as the UK and the USA, highlighting our commitment to global excellence.
We offer a number of different alloys in the 6000 range.
At AMS, we recognise the importance of sourcing sustainable aluminium billet. Our commitment to innovation is geared towards not only meeting but surpassing the demands and expectations for sustainability from our customers and specifiers. We take pride in offering billet options with carbon emissions intensities significantly below the global industry average, affirming our dedication to environmentally responsible practices.
R50 & R75 Billet – 50% & 75% Post Consumer Scrap
- Capable of a minimum 50% & 75% post-consumer scrap content
- Fully traceable
- It is third party certified
- R50 has a carbon footprint of only 2.9kg of CO2e for every kg of aluminium produced
- R75 has a carbon footprint of only 2.3 kg of CO2e for every kg of aluminium produced
Low Carbon Primary Aluminium
- Produced from smelters that use renewable energy. Low carbon primary aluminium has an emissions intensity that is 3x better than the industry average.
- Has a carbon footprint of 4.8kg of CO2e for every kg of metal, including both direct and indirect emissions from mining, refining, smelting, and casting.
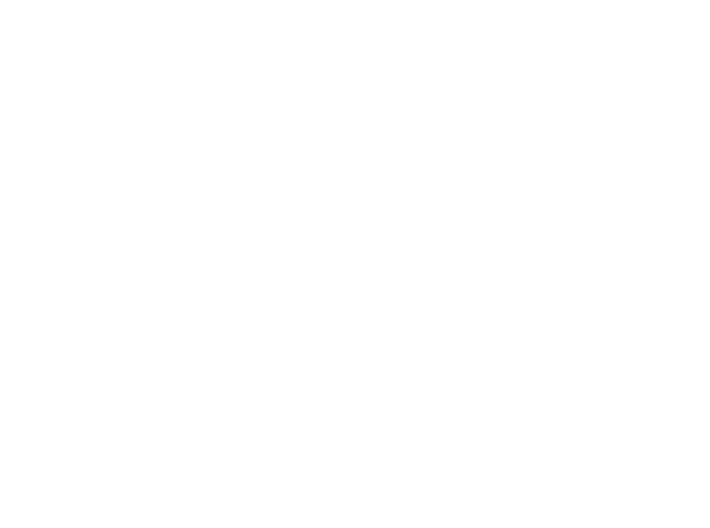
AMS see the many positive benefits in contributing to corportate and social responsibility. Our company is built on the premise of being responsibe through the supply of aluminium products which is 100% recyclable.